Turning traditions into a livable future
The copper refinery in Brixlegg was first mentioned over 550 years ago. They currently employ more than 300 people who are responsible for turning traditions into a liveable future. The Montanwerke Brixlegg. Every year, they recycled 100% of over 160,000 tonnes of copper scrap. Their products: copper cathodes, billets and cakes; precious metals such as gold, silver and platinum; copper oxychloride as the active ingredient in pesticides; and the sandblasting material ‘granos’.

Software for maintenance, warehouse and purchase
“At first, we were only looking for a solution for order processing,” Silvio Turri explains. “But after consulting with the purchasing department, we found that the common preference was a joint solution. The Purchasing department spends 70 to 80% of their time on maintenance only, so it became clear quickly that a total solution was required; software that also includes the warehouse and purchasing. I was immediately pleased with Ultimo’s web-based structure. We eventually made the decision to go with Ultimo Maintenance Management, and we are still very confident we made the right decision. I am still convinced this is the right solution because it allows us to customize input screens, reports and workflows.”
Integration of stock management and purchase
The Production department generates a job, which may be a change, expansion or repairs. This job is linked to an approval process. The relevant department uses the generated job to draw up a cost estimate for the cost unit of the material costs and required hours, which can then choose to either approve of reject the estimate. The active order is now the basis for material orders, issues from the warehouse for spare parts and the hour registration for the departments in question.
The registration of costs is an important topic for Montanwerke Brixlegg, so it is not surprising that this aspect of the integration of Ultimo is extra extensive. For this purpose, an interface with the existing financial accounting system is available, to which all incoming invoices registered in Ultimo are sent. The issuing of materials in the warehouse for spare parts has also been expanded with a barcode scanner so the parts are registered online with the correct repair order. Silvio Turri: “Previously, the stock materials were only issued to the cost unit, but with Ultimo we now have an exact overview of the costs for failures, maintenance and repairs that are assigned to separate pieces of equipment.”
The figures show how successful the integration has been: Over 200 users, 2200 pieces of equipment, 5000 articles, 6000 orders and 14,000 assignments, with approximately 800 being added every month. We now generate information about costs, lead times, downtimes and much more for every new assignment. This information is now analysed because ‘the equipment speaks to us’, and Ultimo helps us understand what they’re saying. There is a very clear trend of fitting preventive maintenance and fewer disruptions.
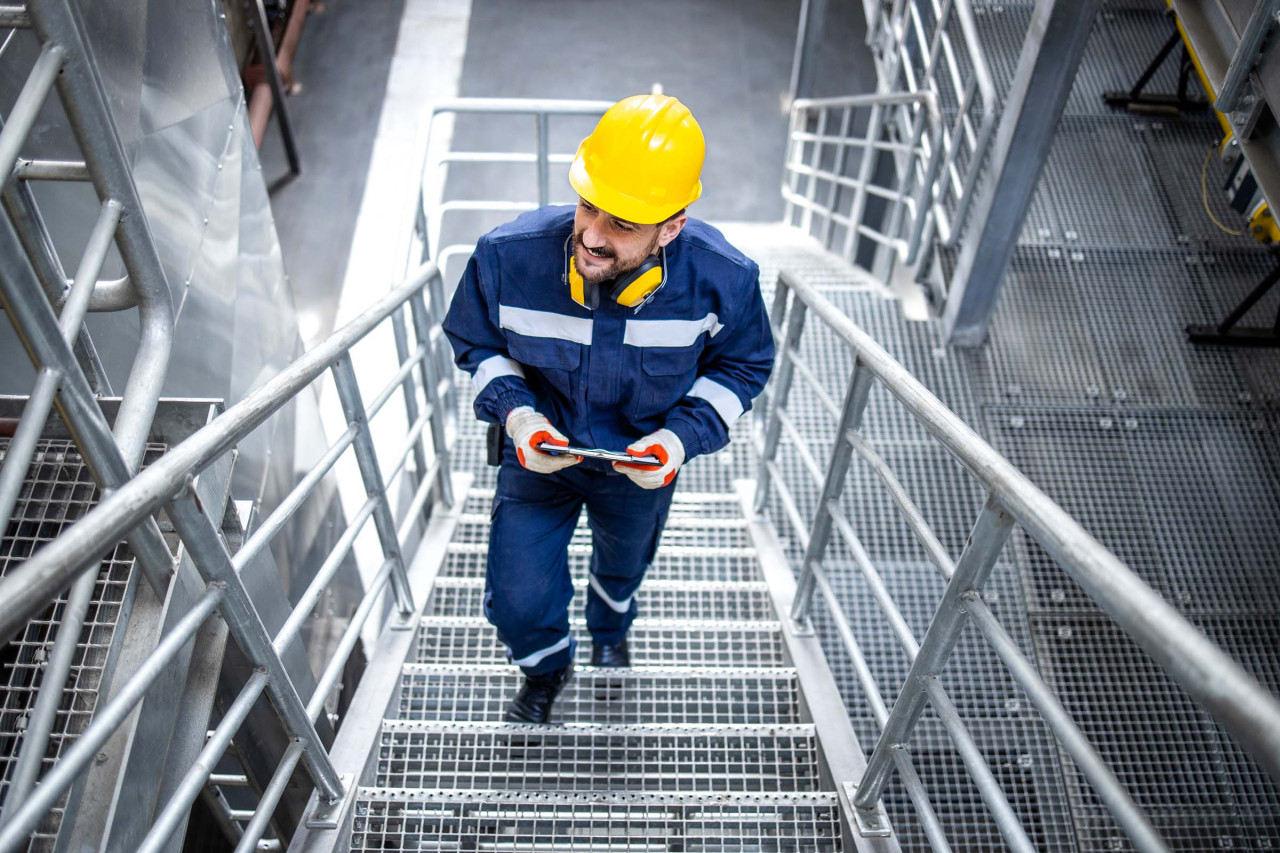
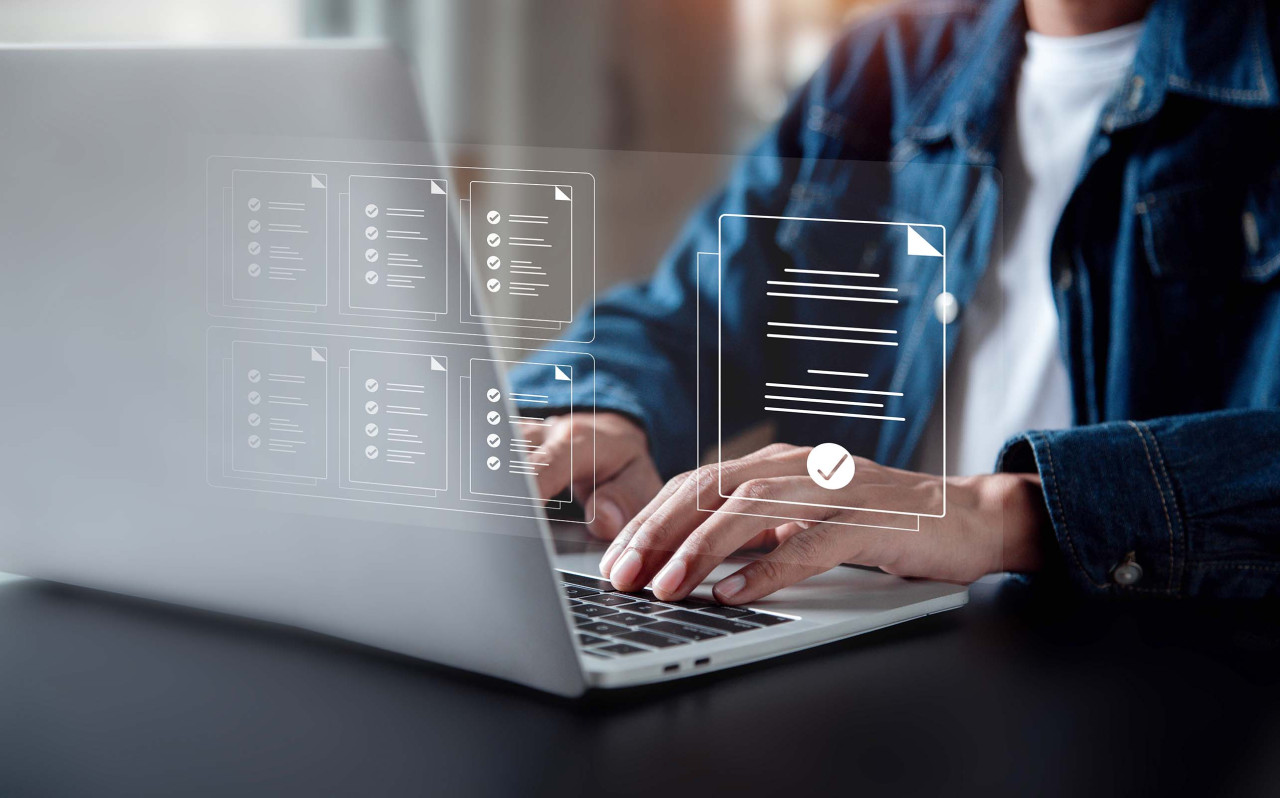
The benefits of Ultimo are very clear
The commissioning of Ultimo necessitated new process flows, but overall the benefits of Ultimo are very clear. “I would put the payback time at around two to three years for our amount of standard processes,” Turri continues. The efficiency in the order processes has been improved which also includes improvements in purchasing, “which I estimate already account for a savings potential of 5% of our purchasing volume every year.” Part of the reason for this are lowered storage costs because of better stock management. On top of that, spare parts are allocated to the assets, meaning we know whether a part is in use or in stock at all times. When equipment is no longer used or necessary, the spare parts that are no longer necessary are also removed from the warehouse.
Let’s connect
Get your questions answered. Schedule a personalized demo to see how Ultimo can add ease and value to your business. No strings attached.