Europe’s leading manufacturer of polystyrene beads
Part of the global BEWI concern, BEWI RAW is Europe’s leading manufacturer of polystyrene beads – the raw material for Expanded Polystyrene (EPS), commonly known as Styrofoam. Its manufacturing facility at Porvoo, Finland, produces a range of EPS products for use as raw material in sectors including insulation and packaging.
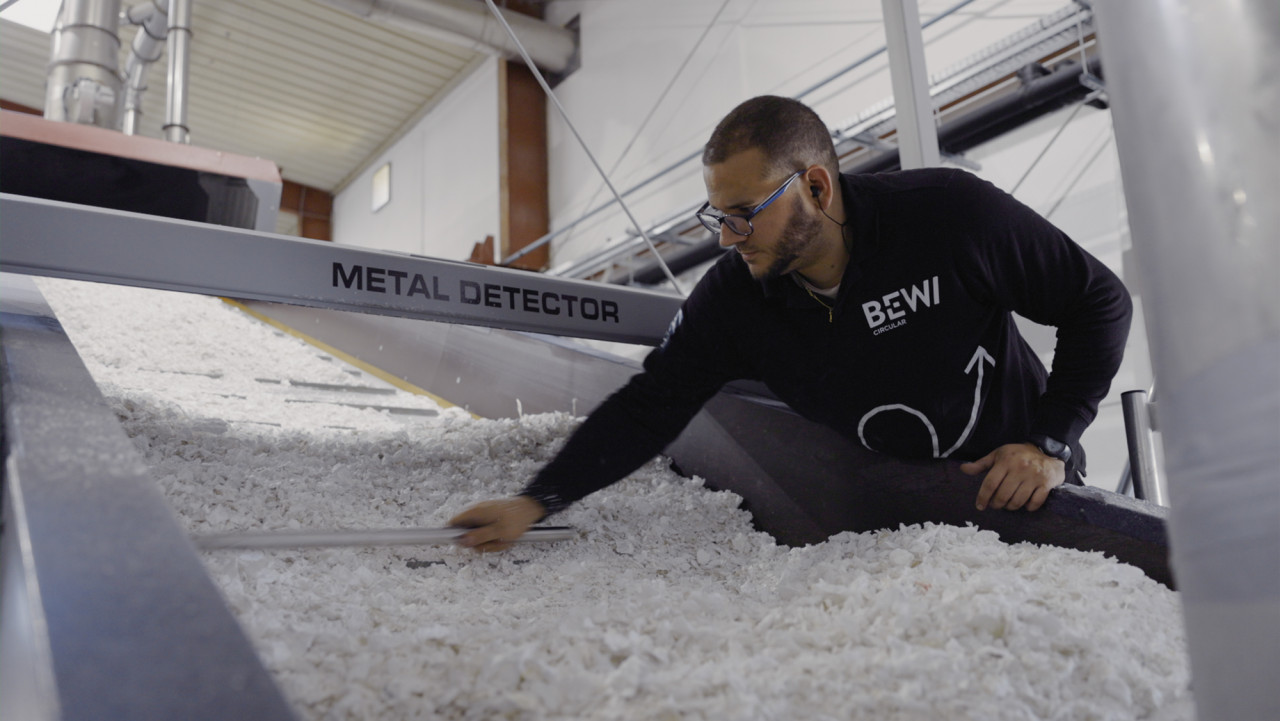
Enabling strategic maintenance planning
Once BEWI RAW made the decision to implement Ultimo CMMS software, both sites agreed to a cloud-based subscription model, including modules for maintenance and HSE. Enabling strategic maintenance planning was the priority for BEWI RAW. The first step was to identify mission-critical tasks and plan their maintenance in Ultimo. Previously, many maintenance tasks were logged on paper, so a comprehensive overview of past maintenance actions, repairs and replacements was hard to obtain. In the hectic production environment, small incidents could also quickly escalate.
First-hand information for minimising disruption.
On one occasion, before BEWI RAW began working with Ultimo, a simple worn-out bearing brought production to a standstill. There was no schedule for inspecting or replacing bearings, which allowed the component to wear out, and consequently damage the machinery. The issue wasn’t noticed until the entire machine broke down, but, unfortunately, replacement parts were no longer available as the equipment originated from the 70s. In the end, the only solution was to replace the entire machine and modify the production line, which was designed to house the older model.
With Ultimo, BEWI RAW can also increase efficiency as operators can raise tickets for maintenance tasks remotely. The maintenance team can then instantly see that a new job has been created and prioritise it accordingly. Having access to first-hand information is essential for minimising disruption.
BEWI RAW is also using Ultimo to simplify reporting, managing everything except financial transactions in the software. Previously, all documentation relating to the production machinery was stored in folders consisting of hundreds of sheets of paper. Now, all asset information, from invoices and work orders and user manuals, will be available in digital form in Ultimo. This will reduce the administrative burden and ensure all vital information is readily available when needed, regardless of whether it will be accessed from the office or the factory floor.
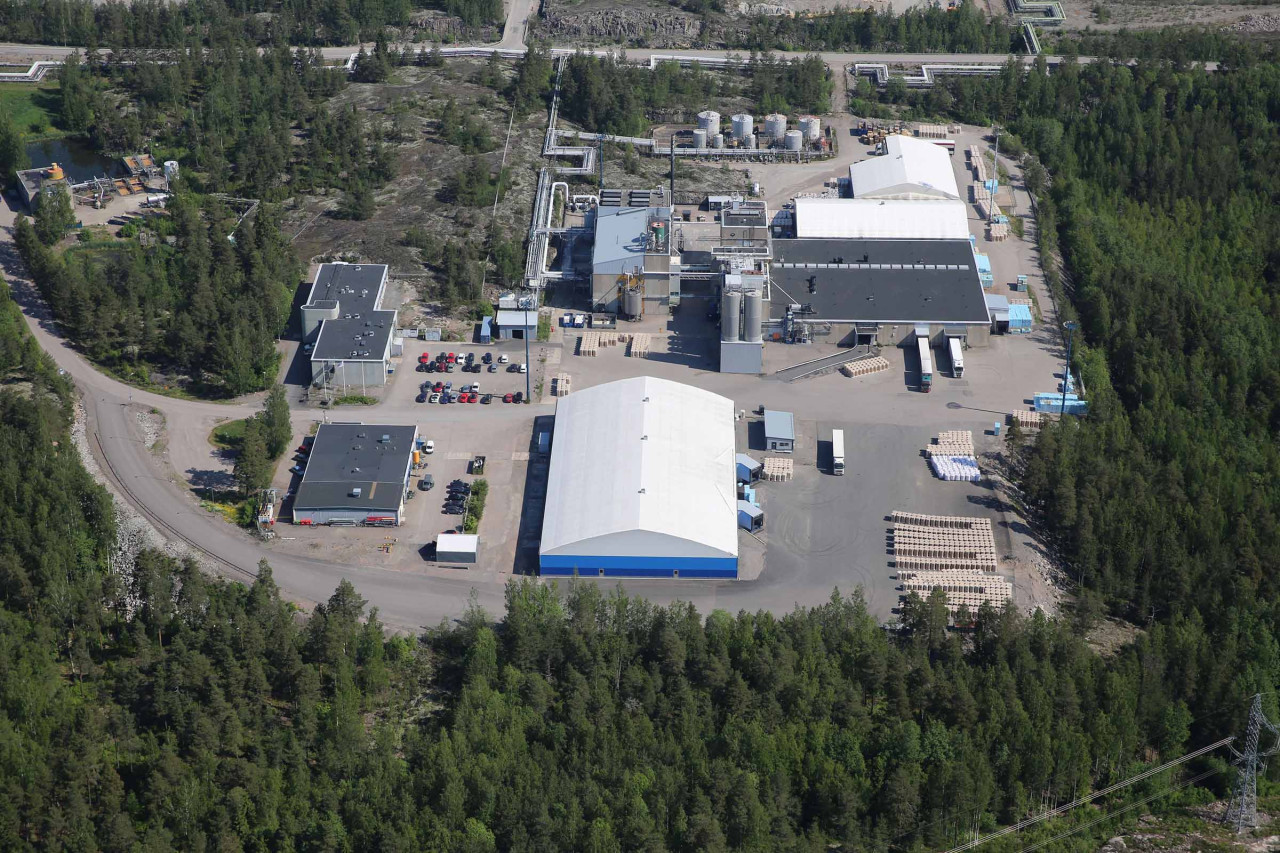
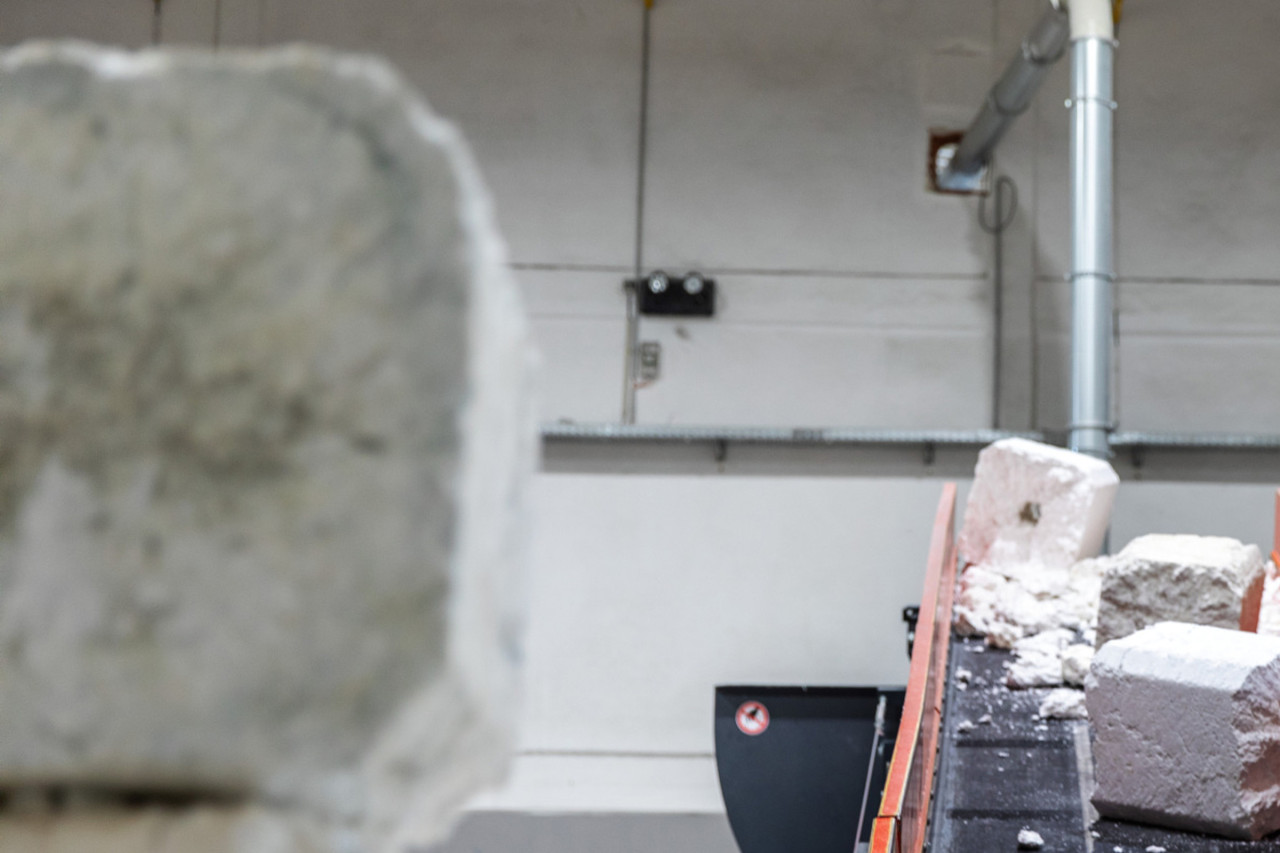
Empowering employees
Overall, the implementation process has gone smoothly. The company is implemented Ultimo’s modules in stages, introducing a new feature approximately every three months. The next step is implementing the HSE module – already successfully implemented by BewiSynbra – which will help simplify the management of critical safety tasks such as logout tagout and work permits. Ultimately, BEWI RAW wants to use Ultimo to enable passive information sharing so that key information, such as job schedules or active work permits, could be displayed in real time on screens in employee break rooms. The goal is to empower employees by giving them direct access to the information they need to do their jobs.

Moving the process forward
“We are not a hierarchic organization where you have to wait to be told what to do. All employees take 100% responsibility for their jobs. With Ultimo, we can make essential information easily available to everyone so they can be even more proactive. The great thing about Ultimo is that you can get started with little knowledge of the system. With some software, you must know everything before getting started, but in Ultimo, anything you do helps move the process forward.“ tells Petri Rekonen, Plant Manager of BEWI RAW OY.
Downloads
-
BEWI RAW download
Let’s connect
Get your questions answered. Schedule a personalized demo to see how Ultimo can add ease and value to your business. No strings attached.