Fast-growing company
Specialising in own-label brands, Agristo has been manufacturing frozen potato products, such as traditional Belgian fries, for the global market since 1986. Based in Harelbeke, Belgium, the fast-growing company has three production sites in the country as well as one in the neighbouring Netherlands, which together produce over 800,000 tonnes of products per year.
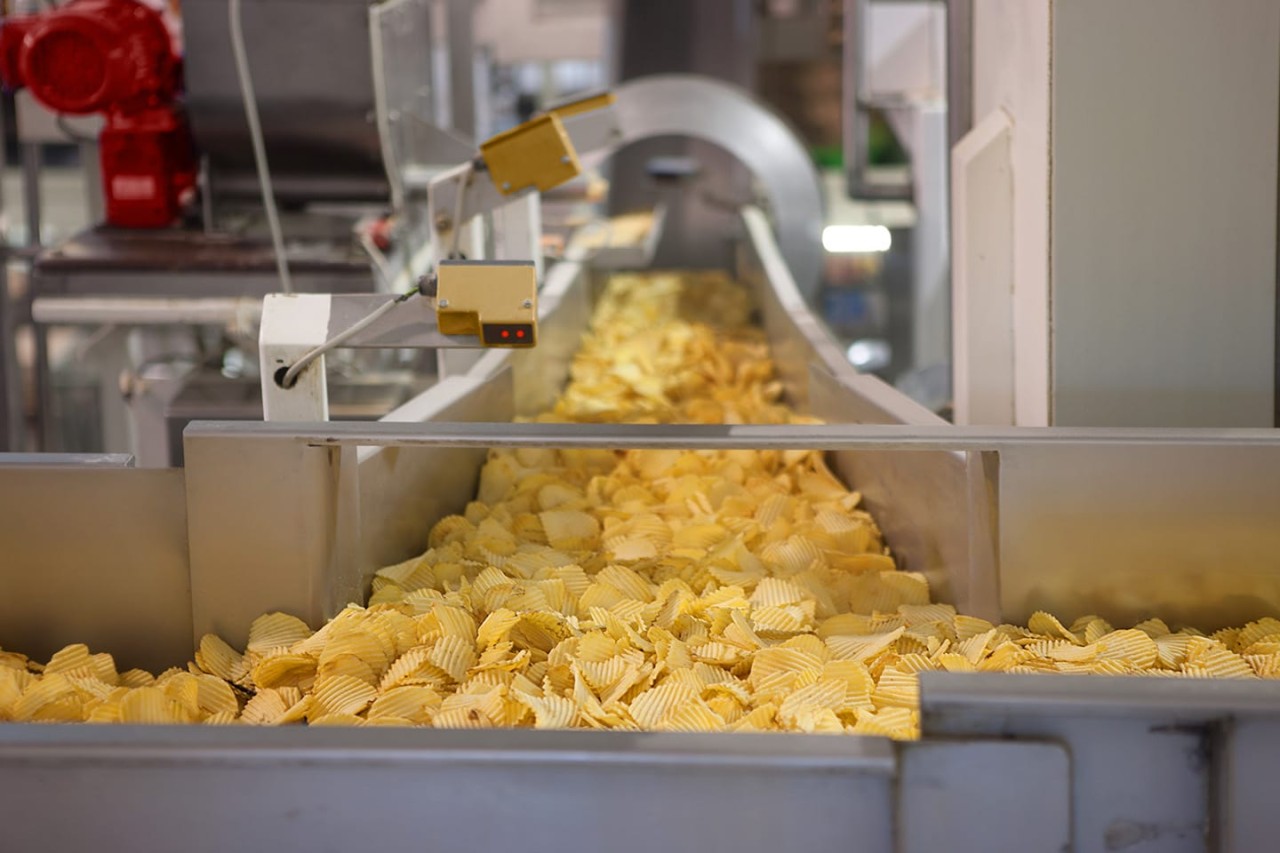
Stay in control
It became clear that the company had grown too big to stay in control of maintenance across all sites, which translated into operational inefficiency. Agristo decided to implement an Enterprise Asset Management (EAM) system to control the maintenance process. After letting the maintenance and production teams compare and rate several providers, it became clear that Ultimo offered all the features the company required.
More structure into the maintenance operation.
The primary purpose of the new software was to implement structure into the maintenance operation. Before, there was a minimal digital log of all maintenance requests and jobs carried out. This made it difficult to analyze the amount of work carried out, manage stock of parts, and stay on top of the condition of the equipment.
Now, every request, action, and resolution is logged into Ultimo. Keeping track of the tasks carried out is simple. In 2020, the year Ultimo was installed at all sites, a total of 53,695 jobs were created and 46,330 completed. This means that over 127 maintenance tasks were performed each day, in a 24-hour-per-day, seven-days-per-week working regime. Agristo has complete visibility over every maintenance job across all facilities, making it easy to stay on top of asset health and benchmark performance.
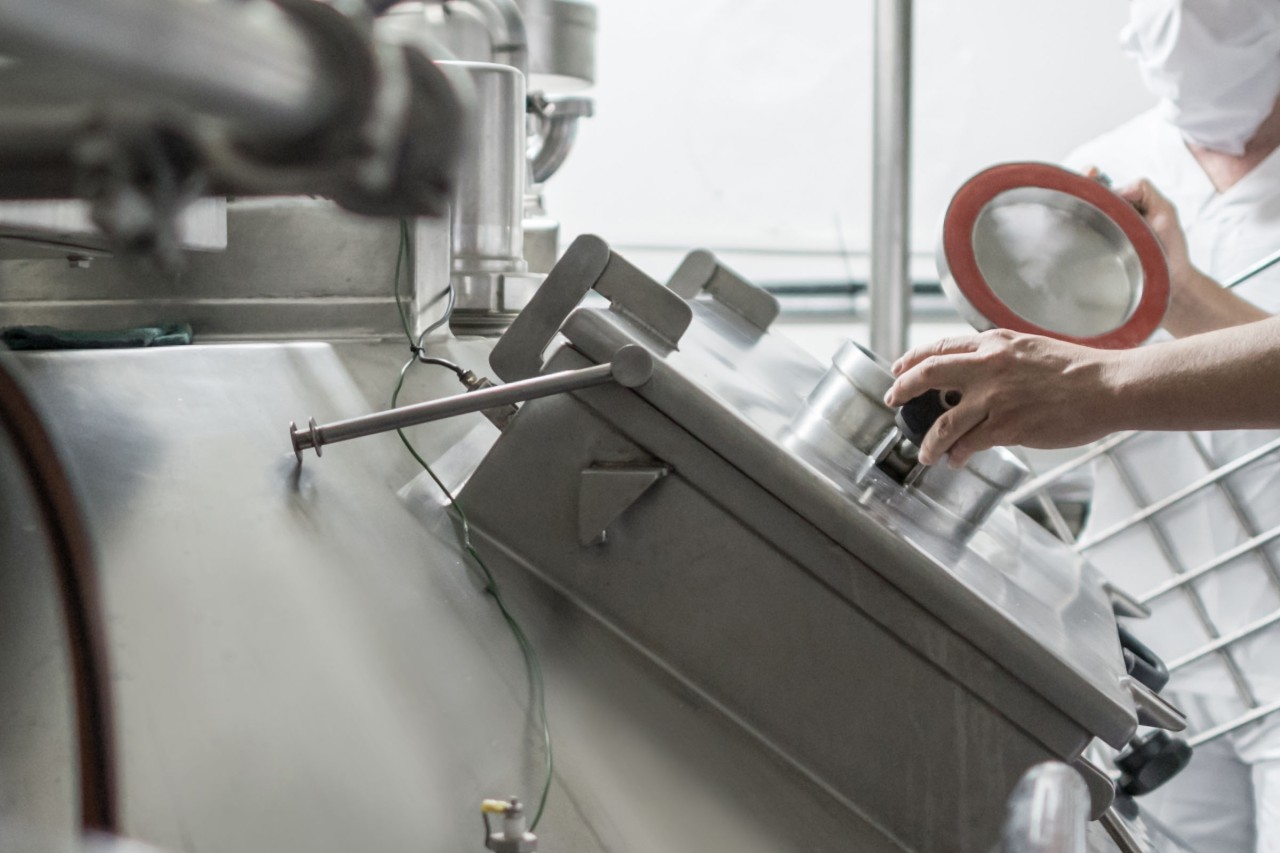
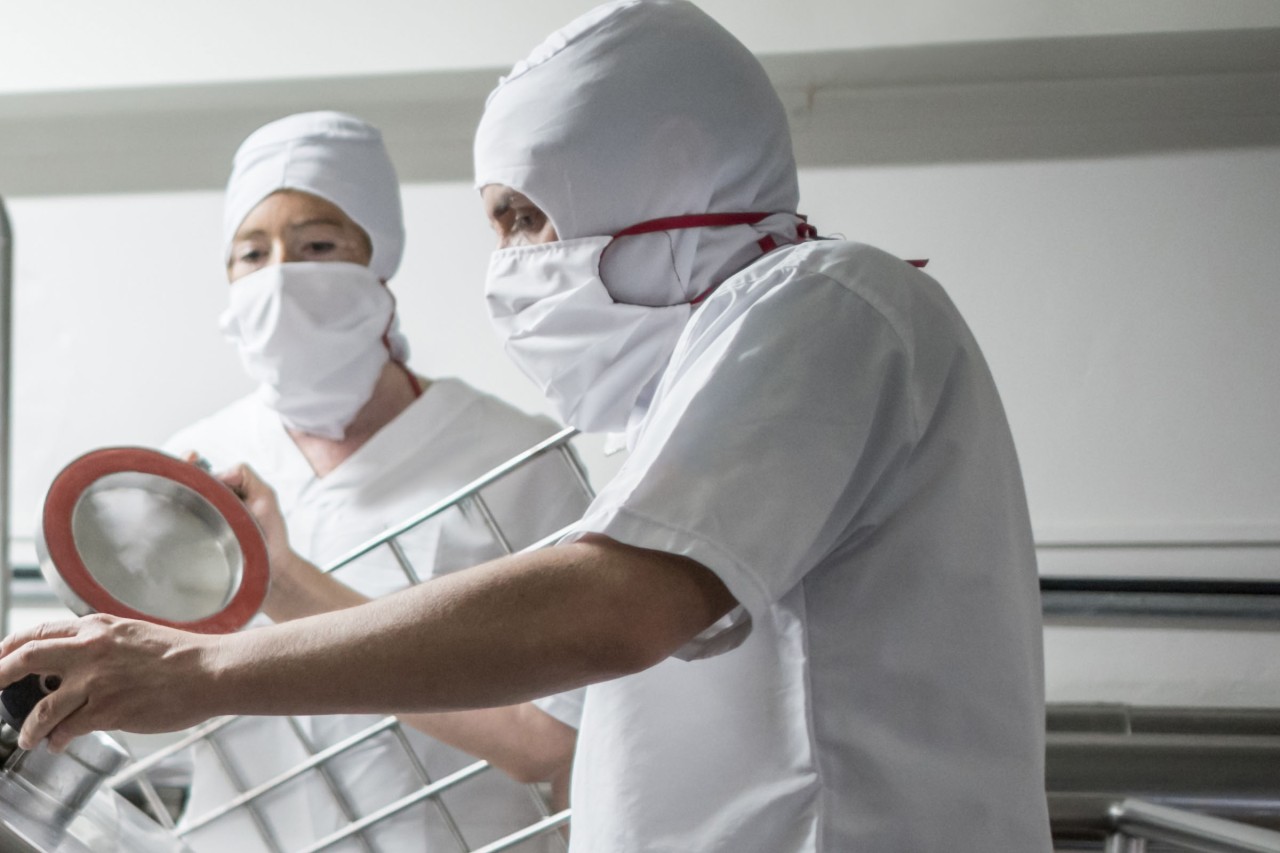
Vital insight into their assets
The maintenance teams can easily view and understand the maintenance status across all the locations to ensure uniform solutions. Agristo gains vital insight into the health of the machines and the efficiency of its production processes, resulting in an estimated increase in uptime of at least five percent. “Being able to show in a clear and structured way how the essential maintenance and safety processes are managed and stored can be a selling point to new customer.” tells Steven Volckaert, Group Maintenance Manager at Agristo.
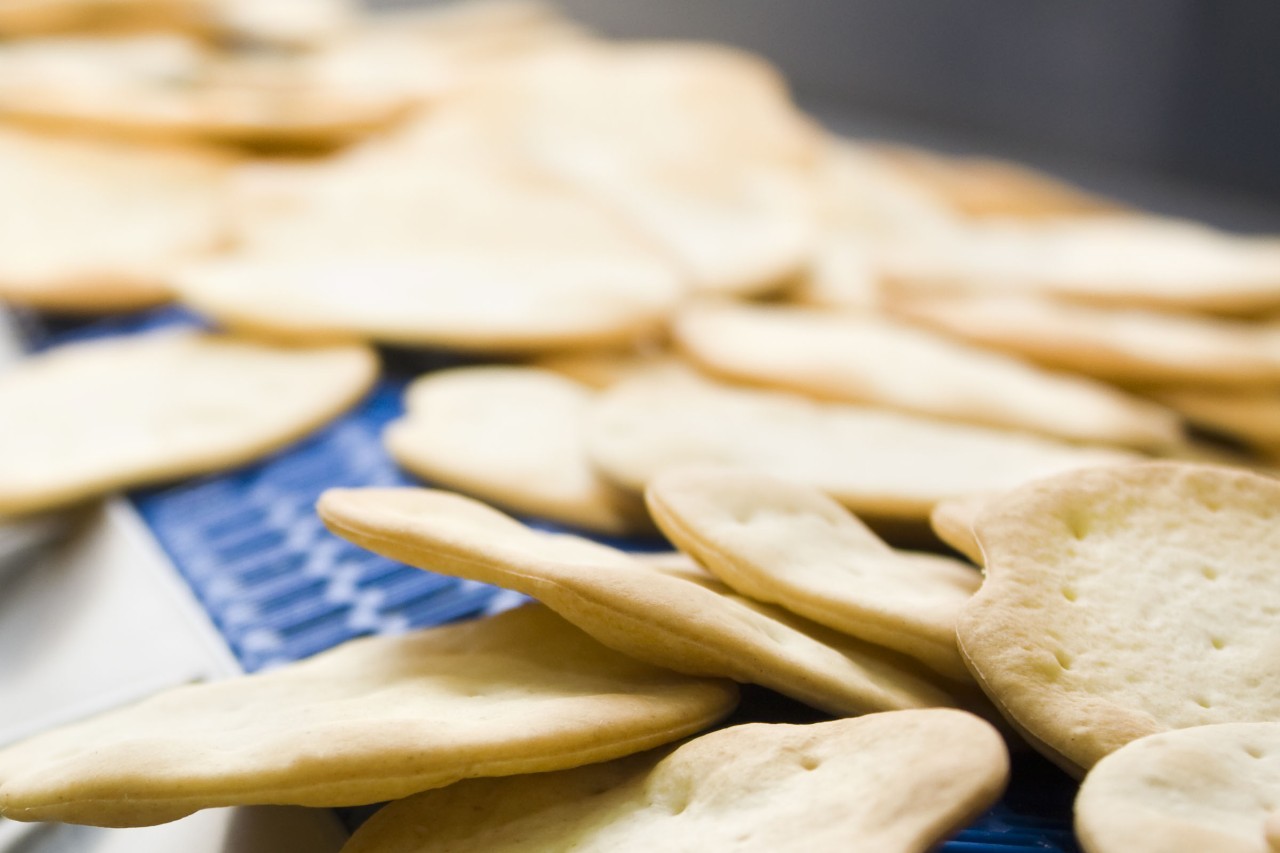
Save time and ensure consistency
Agristo uses Ultimo across operations, making most of the submodules available in the system. For example, it has built a list-based menu to eliminate spelling errors in part names. Before, technicians would type in the name of the part they used. However, the spelling was inconsistent, featuring capitals and misspellings, making the data impossible to analyze. Now technicians select the part name from the list, which saves time and ensures consistency in reporting and stock management.
Downloads
-
Agristo download
Let’s connect
Get your questions answered. Schedule a personalized demo to see how Ultimo can add ease and value to your business. No strings attached.